home » Premium Wall Panels
Are You Looking For Wall panels?
ShuoTai is your go-to source for premium indoor wall panels solutions, adhering to international standards like ISO-9001, ASTM, and CE. Operating 12 state-of-the-art production lines, we cater to a diverse set of applications across sectors such as residential, commercial, and architectural design. Don’t compromise; insist on ShuoTai for quality and innovation.
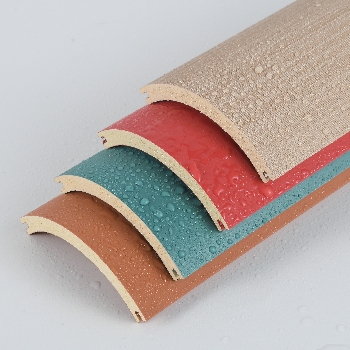
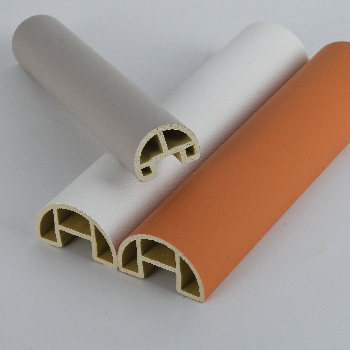
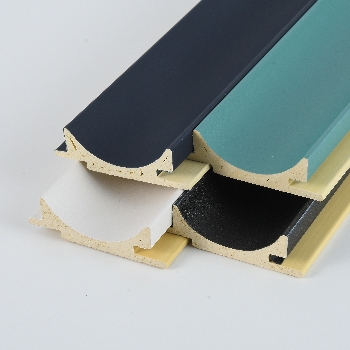
Indoor WPC Wall Panel-85YHB
Indoor WPC Wall Panel-50BY
Indoor WPC Wall Panel-40BY
The Ultimate Guide to Wall Panels
Functions,Materials,Used and More
What Is The Wall Panel?
A wall panel is a pre-fabricated piece of material that serves as a functional or decorative covering for walls. They come in various sizes, materials, and designs, providing an array of options for interior and exterior wall décor. Panels are used to improve the aesthetic appeal, structural integrity, or acoustic and thermal insulation of walls.
Wall panel
What Are the Functions of Wall Panels?
Wall panels serve as a significant element in the design and function of commercial and residential buildings. They not only contribute to the aesthetic appeal of an interior space but also boast several practical functions. Here’s a detailed analysis of the functions wall panels serve:
Aesthetic Enhancement
-
Visual Appeal:
Wall panels come in various designs, textures, and colors, allowing for a vast array of stylistic choices that can elevate the visual aspect of a space. -
Theme Consistency:
They help maintain design continuity and theme consistency in commercial spaces, vital for branding and customer experience. -
Customization:
Custom wall panels can be designed to meet specific artistic visions or thematic requirements, making them ideal for creating unique and memorable environments.
Wall panel
Acoustic Improvement
Sound Absorption:
Indoor acoustic wall panels are designed to absorb sound, which helps in reducing echo and reverberation in a room, contributing to a more comfortable auditory environment.
Noise Reduction:
In areas where noise pollution is a concern, these panels can significantly reduce the intrusion of unwanted sounds, which is crucial for places like conference rooms and theaters.
Functional Utility
Space Definition:
Wall panels can be used to define spaces subtly without the need for full walls, which is particularly useful in open-plan areas.
Hide and Integrate:
They can conceal unsightly elements like wiring or structural components and integrate utilities such as lighting or AV systems seamlessly into the wall design.
Durability and Protection:
Wall panels add a layer of protection to walls, shielding them from damage in high-traffic areas.
Wall panel
Thermal and Environmental Regulation
-
Insulation:
Some wall panels have insulating properties that can help regulate temperature, contributing to the energy efficiency of a building. -
Humidity and Mold Resistance:
Certain materials used in wall panels, like WPC (Wood Plastic Composite), are resistant to humidity and prevent mold growth, ensuring a healthier indoor environment.
Ease of Maintenance
-
Cleanability:
Wall panels are often designed to be easy to clean, requiring minimal maintenance and thus reducing long-term upkeep costs. -
Replaceability:
In the event of damage or wear, individual panels can typically be replaced without the need for extensive work on the entire wall.
Wall panel
Versatility and Innovation
-
Modular Design:
Some wall panels are created with a modular design, allowing for quick installation and flexibility in design changes. -
Integrated Technology:
Panels can come equipped with integrated technological solutions, such as built-in screens or touch panels for smart building management.
Economic Efficiency
-
Cost-Effective Solutions:
Wall panels can be a cost-effective alternative to traditional wall construction and finishing methods. -
Speed of Installation:
The installation process for wall panels is usually faster than traditional methods, reducing labor costs and downtime for businesses.
In summary, wall panels are multifunctional elements that enhance the aesthetic, acoustic, and functional characteristics of a space. They offer versatile solutions that align with the demands of modern architecture and interior design, providing both form and function in a variety of settings. For B2B clients, selecting the right type of wall panel can significantly contribute to the operational efficiency, comfort, and aesthetic value of their commercial or residential projects.
Available Options for Wall Panel Materials
Wall panels are fabricated from a diverse range of materials, each offering unique properties that make them suitable for specific applications and environments. While some panels are crafted for their aesthetic appeal, others are engineered to provide functional benefits such as insulation and soundproofing. Here we discuss the primary materials used in the manufacturing of wall panels offered by ShuoTai.
Solid Wood Wall Panels
Constructed from natural wood, these panels offer unmatched aesthetic appeal along with inherent strength and durability. Suitable for both residential and commercial spaces, they bring a touch of elegance and warmth.
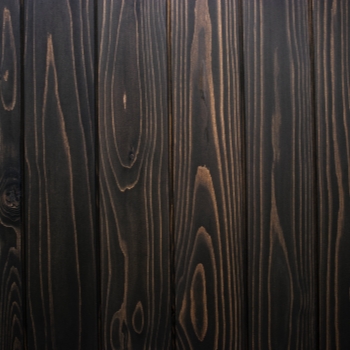
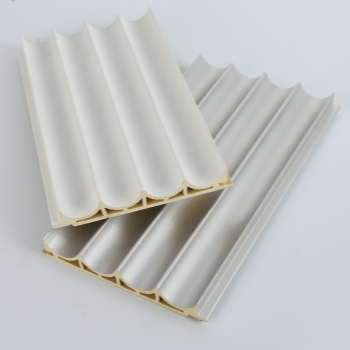
Wood-Plastic Composite (WPC Wall Panels)
WPC wall panels are a blend of wood fibers and plastic polymers, offering the benefits of both materials. These panels are highly durable, water-resistant, and low maintenance, making them ideal for both indoor and outdoor applications.
Metal Wall Panels
Made from metals like aluminum or steel, these panels are known for their durability and strength. Often used in commercial or industrial settings, metal panels are fire-resistant and offer good thermal and acoustic insulation.
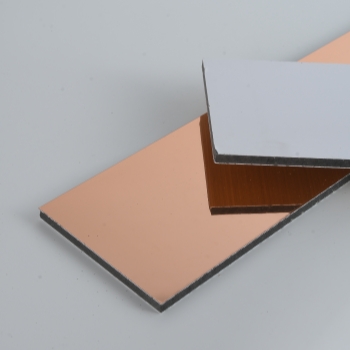
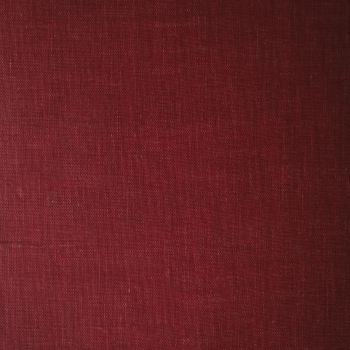
Fabric Wall Panels
Constructed with a core of acoustic foam and a fabric finish, these panels are specifically designed for soundproofing applications. They are lightweight and offer excellent acoustic properties.
Gypsum Wall Panels
Commonly used in commercial interiors, these panels offer excellent fire resistance and acoustic properties. They are typically covered with paper or vinyl and can be painted or finished in various ways.
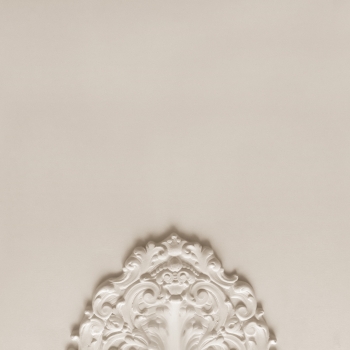

PVC Wall Panels
Made from polyvinyl chloride, these panels are lightweight and water-resistant, making them suitable for bathrooms and kitchens. They offer a cost-effective solution for wall coverings.
Fiberglass Wall Panels
Composed of fine glass fibers, these panels offer excellent thermal insulation. They are often used in commercial and industrial applications where temperature control is a priority.
If you’re interested in fiberglass panels, you might want to keep an eye on these internationally recognized websites that offer quality products, comprehensive services, and useful information.

Understanding the unique properties of each material allows for a more informed decision when choosing wall panels for your project. At ShuoTai, we offer a broad range of top-quality, customizable panels crafted from these materials, each held to the highest standards of quality and performance. Our state-of-the-art manufacturing facilities feature 12 production lines that adhere to stringent quality controls, ensuring that each panel component meets or exceeds industry standards.
Manufacturing Methods Used for Wall Panels

Manufacturing Methods for Wall Panels
Understanding the manufacturing methods for wall panels is essential to ensure you acquire products that meet the standards and expectations of your global clientele. The manufacturing process not only affects the quality and characteristics of the wall panels but also their suitability for specific applications. Here is an in-depth look at the common manufacturing methods used in the production of wall panels:
Veneering
- Pressing: Wood veneers are glued and pressed onto core panels (like MDF or plywood) under high pressure to create a flat, smooth surface.
- Laminating: Similar to veneering but often involves a layer of plastic or vinyl, providing additional colors and patterns.
Composite Panel Fabrication
- Extrusion: Used for WPC and plastic panels where materials are melted and formed into continuous profiles that are then cut to size.
- Compression Molding: Combines fibers and resin, applying heat and pressure to mold into shape—common for fiber cement panels.
Metal Panel Processing
- Roll Forming: Metal sheets are fed through a series of rollers to form into the desired profile and then cut to length.
- Stamping: Metal panels are stamped with high-pressure machinery to create textured or patterned designs.
Lamination
- Hot/Cold Press Lamination: Decorative papers or materials are bonded to substrates under controlled heat and pressure.
- High-Pressure Laminates (HPL): Multiple layers of kraft paper impregnated with resin are bonded together, creating a tough and durable surface.
Molding
- Injection Molding: Used for creating detailed or complex shapes with plastics like PVC.
- Thermoforming: Sheets of plastic are heated and then formed over a mold. This can also be used for solid surface materials like Corian.
Solid Wood Processing
- Milling/CNC Routing: Solid wood panels are shaped and patterned using high-precision CNC machines for intricate designs.
Finishing Processes
- Painting: Automated spray machines apply uniform paint layers, with curing processes to ensure a durable finish.
- Printing: Digital or direct printing can be used to apply designs directly onto the panel surface.
Glass Panel Manufacturing
- Tempering: Glass is heated and then rapidly cooled to increase strength.
- Laminating: Layers of glass are bonded with interlayers under heat and pressure for safety and sound insulation.
Natural Stone Panel Fabrication
- Cutting/Polishing: Stone slabs are cut to size and then polished to the desired finish.
Eco-Friendly Panel Production
- Bamboo Processing: Bamboo is sliced, treated, and pressed to form panels.
- Recycling: Recycled materials are processed to create new panels, often using a combination of compression and heat.
Each method comes with its own set of technical specifications, cost implications, and environmental considerations. As a purchaser, aligning with manufacturers who use the appropriate methods for your product needs is crucial. Whether it’s a high-quality finish, durability, or cost-effectiveness, the manufacturing process plays a key role in delivering the final product that fits the demands of your diverse range of customers. By staying informed about these methods, you can make educated decisions about which products to stock, based on how they’re made, their quality, and their suitability for various applications in different markets.
Below are some international websites where you can find reliable information:
Panel Installation & Maintenance
Installation Guide
-
Preparation:
- Assess the Environment: Check that the installation area is dry, clean, and structurally sound.
- Acclimate the Panels: Allow the panels to acclimate to the room’s temperature and humidity for at least 48 hours before installation.
-
Tools and Materials:
- Necessary Tools: Gather tools such as a level, drill, saw, tape measure, and adhesives/sealants recommended by the manufacturer.
- Hardware & Fixings: Use the correct type of screws, nails, or mounting systems as specified for the panel type.
-
Process:
- Measuring & Cutting: Measure the area precisely and cut the panels to size, accounting for outlets and fixtures.
- Alignment: Start from a corner, using a level to ensure the panels are straight and aligned.
- Fixing Panels: Follow the manufacturer’s guidelines for fixing panels to the wall, which may include adhesives, nails, or an interlocking system.
-
Sealing & Finishing:
- Sealing Joints: Seal any joints or edges to protect against moisture using appropriate sealants.
- Trimming: Apply any necessary trim or molding to create a finished look.
-
Special Considerations:
- Acoustic Panels: These may require additional materials for sound insulation and should be handled according to their acoustic properties.
- Curved Panels: May require a more flexible mounting system and should be handled with care to prevent damage.
Maintenance Guide
-
Cleaning:
- Regular Dusting: Use a soft cloth or duster to remove surface dust.
- Wiping Down: For most panels, a damp cloth with mild detergent will suffice for cleaning. Rinse with a clean, damp cloth afterward.
- Avoid Harsh Chemicals: Do not use abrasive cleaners or solvents that can damage the panel’s finish.
-
Inspection:
- Regular Checks: Inspect the panels regularly for any signs of damage or wear.
- Sealant Integrity: Check sealants and edges for any signs of peeling or cracking.
-
Repair:
- Surface Damage: Small scratches or dents can often be filled in with a repair kit or touched up with matching paint.
- Loose Panels: Address any loose panels immediately to prevent further damage.
-
Preventive Measures:
- Avoid Moisture: Ensure areas with panels are well-ventilated to prevent moisture buildup, which can lead to mold or warping.
- Protect from UV Light: Some panel materials may fade with prolonged exposure to sunlight. Consider UV-protective measures if necessary.
-
Replacement:
- Panel Lifespan: Be aware of the typical lifespan of different panel materials and be prepared to recommend replacement when necessary.
- Sustainable Disposal: Advise on the proper disposal or recycling of panels when they are being replaced.
Providing this comprehensive guide to your customers will not only help them in proper installation and maintenance of the wall panels but will also reinforce your reputation as a knowledgeable and reliable supplier. Ensuring that your clients are well-informed can lead to increased satisfaction and potentially repeat business as they trust your expertise and the quality of your products.
Panel Customization
Panel Customization
Panel customization is an essential aspect of the wall panel industry, especially when catering to diverse client needs in various regions. It involves tailoring wall panel products to meet specific aesthetic, functional, and installation requirements. Here is a detailed analysis of the facets of panel customization:
Customization by Material
- Material Selection: Customize the panel material to match the desired properties, such as moisture resistance, fire retardancy, or acoustic performance.
- Composite Options: Provide options for wood plastic composites (WPC) or other composite materials that offer unique characteristics.
Dimensional Customization
- Size and Thickness: Panels can be cut and adjusted to specific dimensions to fit unique spatial requirements or to create certain visual effects.
- Shape Customization: Panels may be custom-shaped, including options for curved panels to fit specific design schemas.
Aesthetic Customization
- Color Matching: Custom color solutions to match a brand’s identity or design motif using specific paint codes or color systems.
- Texture and Pattern: Offering a variety of textures, from smooth finishes to embossed patterns, to enhance the tactile experience.
- Surface Finishing: Options can include matte, glossy, or satin finishes, as well as specialized coatings for additional functionality.
Performance Customization
- Acoustic Properties: Tailoring the acoustic properties of panels for use in sound-sensitive environments like theaters or conference rooms.
- Thermal Insulation: Customizing the insulative properties of panels to improve energy efficiency in different climate zones.
Installation Customization
- Mounting Options: Providing different mounting systems, like rail or bracket systems, for ease of installation or to meet structural requirements.
- Panel Interlock Design: Designing panels with specific interlocking features for a seamless appearance and improved stability.
Environmental Customization
- Eco-friendly Materials: Customizing panels with materials that are sustainable, such as recycled content or rapidly renewable resources.
- Low-Emission Manufacturing: Offering panels that are manufactured with processes that reduce environmental impact, like low-VOC finishes.
Compliance and Certification
- Regulatory Compliance: Custom panels to meet the building codes and regulations of different regions.
- Certification Matching: Providing panels that meet certain certifications, like LEED or BREEAM, which can be important for projects with environmental goals.
Branding and Identification
- Logo Integration: Incorporating company logos or branding elements directly onto the panel surfaces.
- Identification Systems: Adding labels or identification systems to panels for larger projects to facilitate easy installation and replacement.
As a wall panel purchaser, understanding and communicating these customization options to your manufacturing partners is critical. It allows you to offer tailored solutions to your clients that meet their specific demands, which can range from the aesthetic nuances of design-driven projects to the technical specifications required for high-performance buildings.
By ensuring that your suppliers or manufacturers are capable of delivering on these customization requests, you solidify your position as a provider of specialized wall panel solutions, enhancing customer satisfaction and expanding your market reach. Always emphasize the importance of clear communication regarding the details of customization to avoid errors and ensure that the end product aligns perfectly with the clients’ expectations.
Considerations When Buying Wall Panels
Procurement Considerations for Wall Panels
-
Market Demand Analysis:
- Trends and Preferences: Stay informed about current trends in wall panel designs, textures, and materials in different regions.
- Customer Requirements: Understand the specific needs of your target market, including acoustic properties, fire resistance, and aesthetic preferences.
-
Product Quality and Specifications:
- Durability: Assess the lifespan and wear resistance of the wall panels, ensuring they are suitable for their intended use.
- Performance Characteristics: Consider the functional attributes such as thermal insulation, sound absorption, and moisture resistance.
- Compliance: Ensure the panels meet the building codes and standards required in your customers’ locales.
-
Material Selection:
- Variety of Materials: Offer a range of materials, including wood, MDF, PVC, WPC, metal, and composites, to cater to diverse customer needs.
- Eco-friendly Options: Include sustainable and environmentally friendly materials in your inventory to appeal to eco-conscious buyers.
-
Design and Aesthetics:
- Design Options: Provide a selection of colors, patterns, and textures to satisfy different design schemes and customer tastes.
- Customization Potential: Assess the supplier’s ability to customize products for unique projects or customer requests.
-
Technical Considerations:
- Installation Mechanisms: Ensure the panels come with user-friendly installation methods or systems that are compatible with various building structures.
- Maintenance Needs: Consider the ease of maintenance and cleaning of the panels as this is a significant selling point for end users.
-
Pricing and Profit Margins:
- Cost-Effectiveness: Negotiate favorable purchase prices without compromising on quality to maintain healthy profit margins.
- Volume Discounts: Check if there are pricing advantages for bulk orders that you can pass on to your clients.
-
Supplier Reliability:
- Manufacturing Consistency: Partner with manufacturers known for consistent quality and supply chain reliability.
- Lead Times: Evaluate the supplier’s production and delivery timelines to ensure they align with your inventory turnover rates.
-
Shipping and Handling:
- Packaging: Ensure that the packaging is robust enough to protect the panels during transit.
- Logistics: Consider shipping costs and the efficiency of the supplier’s logistics partners.
-
After-Sale Support:
- Warranties: Secure warranties or guarantees that you can extend to your customers.
- Technical Support: Availability of technical support for you and your customers can be a decisive factor for after-sales service.
-
Legal and Ethical Compliance:
- Certifications: Look for products that come with certifications like FSC for wood panels or LEED compliance for green building materials.
- Ethical Practices: Align with suppliers who follow ethical manufacturing and labor practices.
-
Branding and Packaging:
- Branding Opportunities: Identify if there is scope for white-labeling or co-branding, which can aid in marketing the products.
- Informational Packaging: Packaging that provides clear information and installation instructions can enhance customer satisfaction.
By meticulously considering these factors, you will be well-positioned to select wall panels that will fulfill the expectations of your market segment and sustain the growth and reputation of your business. It is always beneficial to conduct sample testing and seek feedback from potential customers to fine-tune your product offerings.
How to choose a wall panel Supplier / Manufacturer
Strategic Supplier Selection for Wall Panels
Choosing the right wall panel supplier or manufacturer is a strategic decision that can significantly affect the sustainability and profitability of your business. The supplier you select should not only have the capability to provide high-quality products but should also align with your operational needs and customer demands. Here are some strategic steps to take when choosing a wall panel supplier or manufacturer:
1. Assess Your Business Requirements
- Specific Needs: Identify the specific types of wall panels that your customer base demands.
- Volume: Determine the volume of products needed to meet your sales targets and check if the supplier can match that scale.
2. Evaluate the Supplier’s Expertise and Reputation
- Experience in the Industry: Look for a supplier with extensive experience and a deep understanding of wall panels.
- Market Standing: Research their reputation in the market through reviews, testimonials, and industry forums.
3. Verify Quality of Products
- Product Samples: Request samples to evaluate the quality firsthand.
- Quality Control Processes: Understand their quality assurance procedures and whether they comply with international standards.
4. Understand their Manufacturing Capabilities
- Technology and Equipment: Ensure the manufacturer utilizes up-to-date technology and machinery for production.
- Customization: Check if they can customize wall panels according to different specifications or market trends.
5. Check for Certifications and Compliance
- Safety and Environmental Regulations: Make sure the supplier complies with the regulatory requirements of your target markets.
- Certifications: Look for relevant certifications such as ISO, CE, or others that may apply to the wall panel industry.
6. Consider the Cost Factor
- Pricing: Evaluate if the cost of the products aligns with your pricing strategy and allows for a good profit margin.
- Payment Terms: Negotiate payment terms that are favorable for cash flow management.
7. Examine the Supplier’s Sustainability Practices
- Eco-Friendly Options: With an increasing focus on sustainability, check if they offer products made from recycled materials or renewable resources.
8. Analyze their Supply Chain and Delivery Systems
- Lead Times: Ensure that the manufacturer can deliver products within your required timeframe.
- Logistics: Assess their logistical capabilities for delivering products to your location.
9. Assess Communication and Support
- Communication: They should have clear and responsive communication channels.
- Customer Support: Confirm that they offer reliable customer service and after-sales support.
10. Look for Flexibility and Scalability
- Adaptability: The supplier should be able to adapt to market changes and your evolving business needs.
- Scalability: They should have the capacity to scale up production as your business grows.
11. Perform a Risk Assessment
- Financial Stability: Investigate the supplier’s financial health to assess the risk of disruptions.
- Political and Economic Stability: Consider the political and economic stability of the region where the supplier operates.
12. Build a Relationship
- Partnership Approach: Consider suppliers who are willing to build a long-term partnership rather than a transactional relationship.
13. Seek References and Case Studies
- Existing Clients: Ask for references or case studies to understand their working relationships with other clients.
By following these guidelines, you can choose a wall panel supplier or manufacturer that not only meets your current needs but also has the potential to grow with your business, ensuring a stable, long-term supply of quality products for your clients.
Reach us
Whether you have a quick question for one of our products or are ready to take the first step towards your dream house, we’re here for you.
If you already have a sketch of your project, send it in and we’ll get back to you as soon as possible.